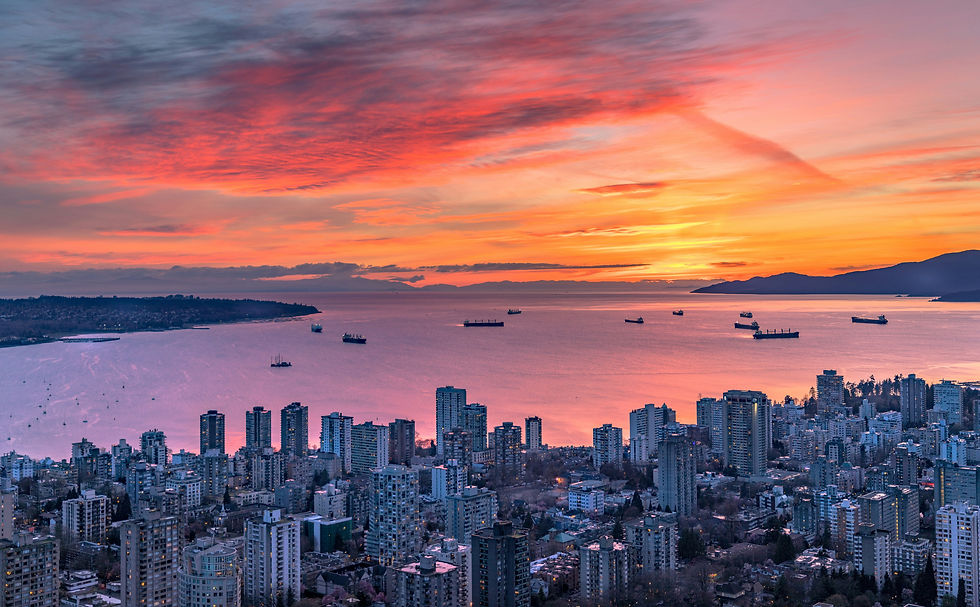
Objective
Ensure the secure and efficient transportation of escalator trusses and components from China to Canada by implementing enhanced packaging and handling protocols. These measures aim to minimize the risk of structural or cargo damage, guaranteeing safe and timely delivery throughout the logistics process.
Key Shipment Details
Incoterm: Ex-Works (EXW)
Point of Origin: Shanghai, China
Final Destination: Vancouver, British Columbia, Canada
Cargo: Escalator trusses and related components
Transport Mode: Ocean Freight
Estimated Transit Time: 15–20 days
Situation
A leading international elevator company was contracted to supply and install escalators for Canada's current commuter railway project in British Columbia. The escalator units, manufactured in Shanghai, China, were oversized, overweight, and required meticulous handling to ensure safe, compliant transport and delivery.
Key Challenges:
Transporting heavy and oversized cargo
Inadequate packaging materials
Underutilization of container space (load optimization needed)
Long-term storage requirements at the project site
Concerns over proper weight distribution within containers
Strict inspection and documentation protocols
Coordination across multiple stakeholders and service providers
Adherence to a tight and non-negotiable delivery timeline
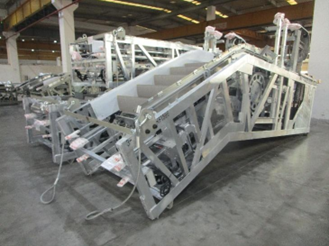
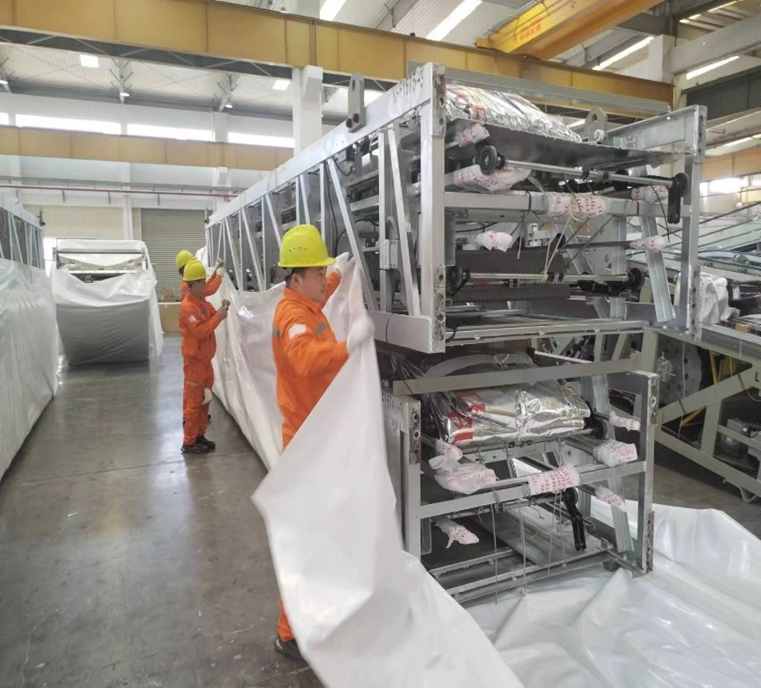

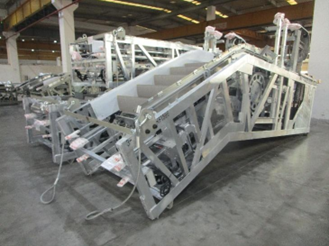
Task
To enable the successful delivery of escalator units for the Broadway Subway Project, the logistics strategy was designed to address packaging integrity, structural safety, regulatory compliance, and time-sensitive execution.
Primary Objectives:
Ensure all packaging met international compliance standards
Safeguard escalator units during extended on-site storage
Optimize weight distribution within each container
Implement visual documentation protocols for transparency
Align all stakeholders on standardized loading procedures (SOPs)
Complete all documentation and insurance formalities on schedule
Meet project delivery milestones without compromising cargo integrity
Provide comprehensive door-to-door cargo insurance coverage
Action
To effectively address the identified challenges and ensure timely, secure delivery of escalator units for the Rail Infrastructure Project, Mentra Logistics executed the following comprehensive action plan:
1. Issued Detailed Packaging Guidelines to the Factory
Mentra Logistics provided clear instructions to avoid the use of cardboard packaging within escalator trusses. All loose items were required to be packed in ISPM 15-certified wooden crates or verified plywood boxes to prevent transit damage. Compliance confirmation was obtained from the shipper in Shanghai prior to loading.
2. Recommended Load Spreaders and Skates for Weight Distribution
Advised the factory to use load spreader bars beneath the truss legs and place trusses on plywood skates with a wider surface area. This ensured even weight distribution, reduced stress on container floors, and enhanced stability during transport.
3. Coordinated Shrink-Wrapping at the Point of Origin
Ensured that each escalator truss was shrink-wrapped at the manufacturing site to protect against environmental elements (dirt, moisture, debris) during long-term outdoor storage at the construction site.
4. Enforced Rigorous Container Inspection Protocols
Mandated a full inspection of container floors, walls, doors, and roofs before loading. Any container showing signs of damage or structural weakness was to be rejected and replaced immediately.
5. Implemented Visual Documentation Workflow
Set up a structured OneDrive folder system for real-time visual documentation at every milestone. The shipper was required to upload photos at three critical stages:
Pre-loading cargo condition
Container inspection
Loading process
Each image set was saved under folders labeled with the respective container number for traceability.
6. Maintained Transparent Communication with All Stakeholders
Facilitated consistent updates and reminders to all involved parties, reinforcing adherence to loading SOPs and documentation protocols throughout the process.
7. Secured Door-to-Door Insurance Coverage
Arranged comprehensive cargo insurance covering the full journey from Shanghai to the final project site in Canada, mitigating any risk of transit-related loss or damage.
8. Pre-Staged Empty Containers at the Factory
Coordinated the advance placement of all required containers at the manufacturing site, ensuring ample time for loading and documentation well ahead of gate cut-off times.
9. Prepared and Finalized Key Shipping Documents
Reviewed and finalized all necessary shipping and compliance documentation, including both House and Master Bills of Lading (HBL & MBL), as well as updated insurance certificates, aligning with the project's logistical and regulatory requirements.
Result
1. All Containers Shipped Successfully
All containers were safely transported from Shanghai to Port Coquitlam, British Columbia, without any incidents.
2. Zero Cargo or Container Damage
Thanks to proper load distribution—using large pads and double-stacked plywood beneath escalator corners—no damage occurred to the cargo or container flooring.
3. Fully Compliant Packaging
All cardboard components were securely packed in ISPM 15-certified wooden crates or plywood boxes, meeting international standards.|
4. On-Site Storage Protection
Escalator trusses arrived shrink-wrapped, safeguarding them from environmental exposure such as mud, dust, and moisture during outdoor storage.
5. Complete Visual Documentation Achieved
Inspection and loading photos were systematically uploaded and organized by container number, providing full traceability.
6. Seamless Stakeholder Coordination
All involved parties—including shipper, booking agents, and consignee—adhered strictly to the agreed SOPs with zero deviations.
7. Insurance & Bill of Lading Finalized On Time
All required documentation, including insurance and shipping documents, were completed before cutoff deadlines, avoiding any delays.
8. On-Time Site Delivery
Escalators were delivered according to the project schedule, supporting the customer’s construction timeline without disruption